第3章 足尾銅山における労働条件の史的分析(続き)
Ⅲ 製煉部門における技術進歩(続き)
3)錬銅工程
銅精製の試行錯誤
水套式熔鉱炉の導入成功に続いて,塩野がとりくんだのは錬銅法の改良であった。吹床でも,洋式熔鉱炉でも,1回の熔解で主として製出されるのは,銅分50%前後の鈹で,これを再度焙焼して硫黄分を減らした上で,木炭やコークスを加えて再熔解し,純度95〜98%の粗銅にしたのである。これが錬銅工程である。錬銅には製鈹と同じ型の熔鉱炉を使用した。1882年まで,製鈹と錬銅は別の吹床を使ったが,83年からは焼鉱と焼鈹を同時に熔解,製煉した。洋式熔鉱炉でも,鉱石と鈹とを同時に装入して製煉し,錬銅と鈹を製出したのである。
なぜ,錬銅工程の改良が必要であったかといえば,燃料消費の節減によるコスト削減もさることながら,足尾銅の品質改善が急務であったからである。周知のように,当時,日本の産銅の大部分は輸出された。当初は粗銅のまま輸出していたが,それでは価格面で不利であり,取引先から品質についての苦情も絶えなかった(30)。このため,1884年,古河は東京市本所区柳原町に粗銅精製用の熔銅所を新設し,精銅の輸出を試みた。本所熔銅所は,塩野の友人である福岡健良(31)が中心となり,大阪造幣局の設備を模した反射炉が設置された。
粗銅は反射炉で熔解され,空気を送入しながら絶えず撹拌することで硫黄,鉄,アンチモニーなどの夾雑物の酸化をうながし,浮上した滓を取り除いた。しかし,このままでは,銅も酸化してしまい展延性を欠くので,最後に送風を止めた上で木炭と松丸太を投入して酸化銅を還元し,これによって純度99.3%の精銅を得たのである。だが,足尾銅は砒素やビスマスなどの含有物が多かったため,反射炉による精製には限界があった。これを解決するため,〈南蛮吹炉〉を設け,鉛を加えて銀分を抽出すると同時に,不純分の除去に努めた。しかし,これでも足尾銅の品質に対する苦情は絶えなかった。
この問題を根本的に解決する方法として追求されたのが電気精銅である。1889(明治22)年5月,本所熔銅所内に8キロワットの発電機が据え付けられ,試験操業を開始した。日本における電気精銅の嚆矢である。その後も実験を続けた結果,ほぼ実用化のめどがつき,1897(明治30)年6月,同所内に電気分銅工場を新設し,翌年1月から操業が開始された。35キロワットの火力発電機が設置され,116の電解槽に送電した。しかし,その処理能力は低く,本格操業を開始してから5年後の1903(明治36)年で年産60トン,1905年で120トン程度であった(32)。これでは足尾産銅の10%〜20%弱に過ぎない。まして,電気精銅がまだ実験段階であった1890年代では,これが足尾銅の品質改善の決め手となる見込みはさだかではなかった。
ベセマ錬銅法
ここで注目されたのが,塩野門之助がかねて実験を続けていたベセマ錬銅法である。ベセマ法は,もともとは銑鉄を可鍛鉄にかえる製鋼法で,1855年にイギリスのヘンリー・ベセマーが特許を得た発明である。熔けた銑鉄の湯の中に空気を吹き込む事によって,銑鉄中の不純物を酸化させて除去するものである。さらに,ベセマーはこれを固定炉でなく転炉で実用化し,1860年にその特許を得た。1880年,マンネスはベセマ法を銅精製に応用することに成功した。マンネスは,塩野が住友別子銅山から派遣されて学んだフランスのサン・テチュンヌ鉱山学校の先輩で,ベセマ錬銅法の成功は塩野が同校在学中のことであった。塩野は当然これに注目し,足尾に移ってからも,その研究を続けていたのである。1891年1月,足尾銅山小滝分局長,木部末次郎の名で「製煉法之儀ニ付伺」と題する文書が提出され,ベセマ錬銅法の採用を提言した(33)。提言は,ベセマ法で1ヵ月30万斤(178.5トン)を錬銅すれば,高炉による錬銅より1ヵ月2,258円94銭,1年間で2万7,107円28銭のコストを節減し,同法採用にともなう起業費1万5,000円は1年以内に償却し得ると試算した上で,「間接の利」として次の諸点を挙げていた。
「一 鉱炉仕働上ニ於テ出鈹ヲ粒状板状又ハ薄片ト為スノ手数ヲ省キ従テ人工ヲ減シ且仕働上ノ消失ヲ除キ得ル事
一 野焼上焙焼上粉砕上運搬上ニ於テ飛散流出消耗スルヲ除キ得ル事
一 広大ナル野焼地所ヲ要スルナク焙焼炉ノ不足ヲ感スルコトナシ
一 本所熔銅所ニ精製シ二回ノ鎔解ヲ為スヘキヲ一回ニ減シ得,従テ経費ヲ減スル事
一 白味〔白目──アンチモンと砒素の化合物〕ヲ除去シ得ルヲ以テ再度之カ分銅法ヲ要セサル事
一 荒銅ニ比シ含蓄微量ナルヲ以テ運搬費ヲ減スルコト
一 銅質善良ニシテ延地銅ト為シ得従テ品位価格ヲ高ムル事」。
古河市兵衛はすぐにこの提言を容れ,翌2月には塩野をアメリカに派遣し,当時世界でただ1箇所ベセマ錬銅法を実用化していたモンタナ州ビュート銅山のパロット製錬所を視察させた。この視察は塩野の希望によるものであったという。おそらく塩野の力では,というより当時の日本の技術水準では,転炉というまったく新しい形式の炉を実用化することは容易でなかったであろう。ベセマ法では,炉は地上に固定されるのではなく,瓶状の炉を中空で支え,炉を回転させて傾け,鍰や熔銅を流出させる必要があった。炉の本体,内容物あわせて数トンもの重量物を安全に傾け得る構造物を設計することは,塩野の力に余ったと思われる。また,熔けた湯の中に送風するには,高圧の送風機を必要とした。これを自力で開発することも困難であったに相違ない。1891年5月,塩野は転炉や送風機の図面を入手して帰国した。この図面をもとに転炉は石川島造船所に発注され,送風機は,塩野をパロット製錬所に紹介したシカゴのフレイザー・アンド・チャルマー社から購入された。
この転炉工場は,木部の名で提言された小滝ではなく,本山の直利橋製錬所の一部に設けられた。その竣工は1893年5月,塩野の帰国から実に2年後のことである。さらに実際の操業開始は,その半年後の同年11月26日であった。転炉の建設,操業がいかに技術的に困難なものであったかがうかがえる。
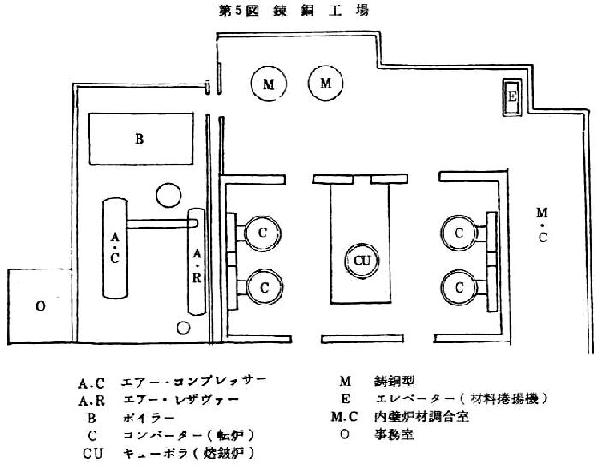
工場には鈹を熔解するためのキューポラ〔熔鈹炉〕が1基,転炉4基が設置された。キューポラは転炉のレベルより2メートル30センチ嵩上された基盤の上に築かれ,熔鈹は鉄製の樋によって転炉に装入された。「木部提言」では熔鉱炉で製出された鈹をそのまま転炉に装入することとしていたから,キューポラは不要であった。しかし,直利橋製錬所では,カラミをそのまま川に廃棄する便宜と,おそらくは水車を動かすのに必要な落差をとるため,熔鉱炉はすべて構内のもっとも低い地域に立地していた。このため,転炉工場は熔鉱炉より6メートルも高い場所に設けざるを得なかった(34)。したがって,鈹はいったん冷却され,砕かれた上で,キューポラで再び熔解されたのである。「木部提言」が「間接の利」として指摘したもののいくつかは実現しなかったのである。しかしベセマ転炉の導入は成果をあげた。足尾銅の品位は93%台から99%前後にあがった(35)。砒素やビスマスの除去によって品質も改善された(36)。鈹を焙焼する必要がなくなったため,製煉に必要な日数は約15日間短縮された(37)。焙焼炉の一部が不要になったことも,工場用地が狭い足尾では大きな意味をもった。
1894年ではベセマ銅は足尾産銅全体の36.8%を占めただけであったが,翌95年になると66.7%に,98年ではついに92.85%となり1,000万斤の大台をこえた(38)。転炉の増設といった設備面での変化がなかったにもかかわらず,ベセマ銅の産出量が年々増大したのは,技術者や労働者が新しい技術を修得するのにかなりの長期間を必要とすることを示している。とくに,製煉部門のように,工程の成否に影響を及ぼす要因が多く,しかも相互に複雑に関連し合っている場合には,生産が軌道に乗るのに数年を要することは珍しくない。もっとも,1897年から98年にかけての急増は,転炉の内壁の炉材を,珪石70%・粘土30%の混合物から,足尾山内で産出する石英粗面岩のブロックの組合せに代えて耐久性を増したこと,またこれにともなって,当初は4基の転炉を交代で1基ずつ稼働していたものを,同時に2基用いて操業するようになったためであった。
【注】
(30) 五日会編『古河市兵衛翁伝』158ページ。なお,古河銅の品質改善について,1884年に外遊した陸奥宗光の調査・進言があったことについては,古河鉱業株式会社『創業100年史』112〜114ページ参照。また,ベセマー錬銅法採用の主たる動機が銅質の改善にあったことは,市兵衛自身がつぎのように語っている。「シンジケートの時に勝利を得ました為めに,随分品物に苦情を附けられて,品位が悪いの性質が悪いのと,色々製煉のことに就いて苦情を受けましたから,何とかこの銅の精製ということには一層の改良を加えねばならぬといふことを考へました。そこでまた技師を亜米利加モンタナ地方へ派遣しまして,段々取調べた結果,ベセマー式で製煉するといふことが,一番簡単で,銅中の汚物を全く除き去るといふことが出来るといふ報告を得まして……」(五日会『翁の直話』1926年,66ページ)。
(31) 福岡健良は1856(安政3)年6月15日,武蔵国榛沢郡(埼玉県)深谷町に生まれた。1872(明治5)年に上京し,大熊春吉の壬申義塾で究理(物理),数学,ドイツ語を学んだ。1874(明治7)年9月,鉱山寮鉱山師長ゴッドフレイの試験を受け,等外二等出仕に採用された(鉱山寮第2回技術見習生であろう)。
間もなく十四等出仕,技術心得を命ぜられ,ドイツ人のお雇い外人・器械師チャーレス・バックメーヤとともに小野組鉱山部所有の鉱山機械調査員を命ぜられた。75年4月,バックメーヤとともに小坂鉱山に転勤。同年10月からは小坂支庁鉱山師兼製鉱師クルトー・ネットーに師事した。1876年2月,ネットーに従って上京。同年依願退職。1878年第一国立銀行に入り,「実地簿記学」を修業し,かたわら「経済学を研究」した。当時福岡は同郷の先輩である渋沢栄一の家に寄食しており,ここで古河市兵衛と相知り,1879年古河に入った。はじめ,九郎畑銀山,ついで軽井沢銀山を経て,草倉銅山に転じ,製煉係となった。1884年,銅精製工場の新設を担当するため上京,東京大学理学部の旧師ネットーの教えを乞うと同時に85年3月から5月にかけ大阪造幣局を見学し,銅精製の実際を学んだ。本所熔銅所の設立後は,所長として,銅精製に当たるとともに,電気精銅の実用化,伸銅場の設立などに従事した。1897年,古河二等支配人,1903年本店理事となった。1905年6月23日病死(『古河文書第33巻〈諸家筆影〉付録,功労者略伝,再稿』栃木県立図書館所蔵)。なお,本所熔銅所については福岡健良「古河鎔銅所事業ノ略記」(『日本鉱業会誌』第82〜84号,1891年12月〜92年2月,『栃木県史』史料編・近現代九,141〜14ページ)参照。
(32) 日本工学会『明治工業史・鉱業篇』(啓明会,1930年)544ページ。
(33) 古河鉱業株式会社『創業100年史』140〜141ページによる。なお,同書は,ベセマー法採用の提言が木部末次郎の名で出ていることから,あたかもこれを木部個人の意見であるかのように述べている。しかし,木部は小野組,山形県,第六国立銀行を経て古河家に入り,足尾では主として会計経理を担当していた人物である。ベセマー法について,このような具体的な提言をなしうる能力をもっていたとは考えられない。
(34) 転炉の導入と同時に,小型熔鉱炉4座を取り壊し,その場所に中型熔鉱炉2座が建設されていることを考えると,熔鉱炉を上段に,転炉を下段に設けることは不可能ではなかったと思われる。何故そうしなかったのか,疑問が残る。考えられる理由は,転炉作業と熔鉱作業はそれぞれ独自のリズムがあり,双方の作業のタイミングを合わせるのは容易でなかったからであろう。これに対し熔鈹炉を使えば,転炉作業に合わせて作業をすすめることができた。
(35)「足尾銅山製煉所沿革」(『栃木県史』史料編・近現代九,112,114ページ)。
(36) 1888年の足尾産粗銅の分析結果では,砒素1.0989%,1891年では2.1683%にも達している(『栃木県史』史料編・近現代九,112ページ)。これに対し,1904年のベセマー銅の分析結果では,砒素の含有量は0.0319%,アンチモンは0.0126%となっている(K.Denawa " Report on the Metallurgical Works of Ashio Copper Mine " 1904, p.171,東京大学工学部金属工学研究科図書室所蔵)。
(37) 『古河市兵衛翁伝』などの著者,茂野吉之助は,ベセマ法の成功によって,「従来,鉱石より製銅に至るまで三十二日を要したものが,この新製煉法によると焼鈹の作業を廃する為め,僅かに二日で事足りた」と記している(同書210ページ)。この記述はその後,技術史の研究書を含めさまざまな文献に引用されている。しかし,焼鈹工程をなくすことで節約し得た日数はせいぜい15日間である。所要日数32日はおそらく土竈を用いて焼鉱していた時代の数字であろう。反射炉による焙焼で焼鉱日数が2週間以上短縮され,さらに転炉の導入によって約15日が節約されたのである。
(38) 「足尾銅山製煉所沿革」(『栃木県史』史料編・近現代九,115〜116ページ)。
[初版は東京大学出版会から1988年5月10日刊行]
[本著作集掲載 2006年3月16日]
【最終更新:
|